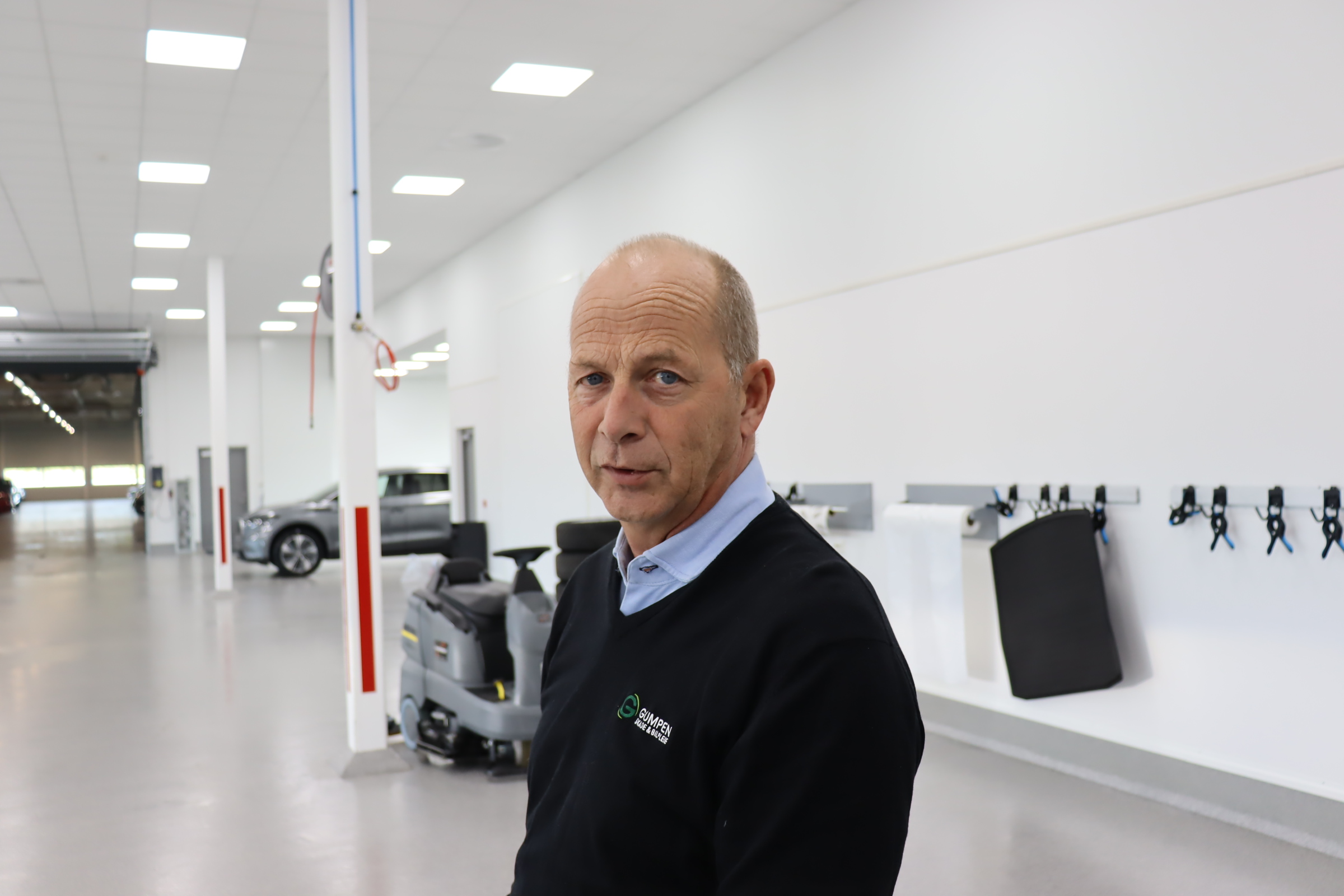
Et mer bærekraftig karosseri- og bilpleiesenter finnes ikke
Fra utsiden ser Gumpen Skade & Bilpleie, Gumpens nye storstue i Sørlandsparken, ut som et helt vanlig næringsbygg. På innsiden er bygget spekket med teknologiske nyvinninger som gjør bygget til det mest bærekraftige karosseri- og bilpleiesenteret som finnes, med svært lave og på noen områder også null miljøavtrykk.
– Da vi ville bygge et nytt skade- og bilpleiesenter, ønsket vi på flere områder å implementere teknologiske og miljømessige løsninger som ikke fantes fra før, alt for å sikre null utslipp og så lave miljømessige påvirkninger for ansatte, natur og miljøet som overhodet mulig, fremholder Terje Olsen som er daglig leder ved Gumpen Skade & Bilpleie.

Norges mest bærekraftige anlegg
Planleggingen av det nye bygget som er på 6.250 kvadratmeter startet i 2016.
– Vi så det var et økt behov for spesialisering innen bransjen, og med nye krav fra myndigheter, forsikringsbransjen og kundene, om en annen type kompetanse, forklarer Terje Olsen, daglig leder ved Gumpen Skade & Bilpleie.
Elektrifiseringen av bilparken medførte at mye snudde granske brått for dem som driver i denne bransjen.
– Vi så er klart behov for å samle alt av bilskade hos alle Gumpen-verkstedene på én plass, og bygde det nye anlegget som er Norges største i sitt slag, og i hvert fall Norges mest bærekraftige anlegg, utdyper Olsen.
En helt ny måte å tenke på
En driver i hele prosjektet har vært økt bærekraft, og med å satse på nye energiformer og en ny måte å tenke og å gjøre arbeidsoppgavene på, for rett og slett stå best mulig rustet for å møte fremtiden. Kravene som ble satt til de løsningene bygget skulle romme ble svært strenge. Det ble besluttet å anlegge 2.500 kvadratmeter med solceller på taket, og å koble seg på fjernvarmeanlegget fra gaten som gir konstant 80 grader i bygget, i tillegg til deres egen varmekilde som fyres opp med energi fra solcellene.

Ekstremt fokus
Videre kom batteribank på resirkulerte bilbatterier for å unngå å kjøpe nye litiumbatterier som belaster miljøet, en parkeringsplass med egen brønn for ikke å belaste det kommunale vann- og avløpsnettet med overvann, men lede vannet tilbake til grunnen for å ha en vannkilde til plenene, frukttrærne og prydbuskene som omkranser bygget.
– Vi har hatt et ekstremt fokus på bærekraft gjennom hele prosessen, på innkjøp og planlegging. I valg av produkter har bærekraft og miljø prioritet nummer én. De leverandørene som ikke kunne leverte på dette, ble heller ikke invitert til å gi en pris på leveransene de kunne tilby, sier Olsen.
Måles på bærekraft og avtrykk
Både på vask, kjemi og lakk ble leverandørene selektert på forhånd ut i fra bærekraft. Olsen påpeker at i det store bildet er lønnsomt å drive slik, både rent økonomisk, og ikke minst i forhold til økt trivsel hos medarbeiderne.
– Vi måles også på rekrutteringsevne og selvfølgelig også bærekraft og avtrykk. I det bildet er det gir bygget en lønnsom drift, selv om det var en dyr måte å bygge på. Her er det ingen ideer som ikke er blitt videreført fordi løsningene ville blitt for dyre.

Sikre egne fagfolk
Hvordan bygget er reist og de løsningene som er valgt, har også mye å si når det kommer til rekruttering av nye fagarbeidere. Olsen viser til at mange har en forestilling om at et lakkeringsverksted er en belastning for miljøet og medarbeiderne.
– Vi har jobbet tett med opplæringskontoret, da vi ser at den nye generasjonen tenker helt annerledes omkring dette. På grunn av ryktet bransjen har, har det ikke vært fagfolk å få tak i. vi er helt avhengig av å produsere egne fagfolk som får jobbe i et rent, godt og tilrettelagt bygg hvor det i alle løsninger har vært og er sterkt fokus på miljø og bærekraft, sier han.
Totalt arbeider det 47 medarbeidere i bygget, hvorav tre lærlinger. Målet er at 10 prosent av arbeidsstokken skal være lærlinger.
– Så, vi leter fortsatt etter gode kandidater, sier Terje Olsen.

Stilte strenge krav
Når det kommer til de teknologiske løsningene som er blitt valgt, har Gumpen Skade & Bilpleie vært pionerer for hele bransjen hvor vi har stilt krav til teknologi og miljøløsninger som ikke var der tidligere, utdyper han.
– Vi vet behovet, hva vi skal utføre, og vi vet hva de negative miljøpåvirkningene historisk sett har vært. Disse er nå blitt løst, slår han fast.
Det betyr at alt av aggregater, maskiner og motorer er blitt bygget inne, og belaster ikke medarbeiderne med støy. Noen enorme aggregater hvor viftene går med moderat hastighet og minimalt energiforbruk, og ikke går for fullt, gjør at anlegget bruker betydelig mindre strøm til å varme opp lakkerings- og varmeboksene, med stor gevinst når det kommer til redusert energibruk.

Det gjør at man også sparer tid. Arbeidsoppgavene blir utført på kortere tid
– Vi sparer tid og mye penger i en lakkprosess som gir null i miljøutslipp og som ikke utsetter medarbeiderne for miljøbelastning. Vi har dermed redusert miljøavtrykket vårt med 65 prosent, energiforbruket er gått kraftig ned, sier han.

For ikke å belaste avløpsnettet, er det blitt bygget et eget anlegg tilrettelagt for resirkulering av vann som gjør at Gumpen Skade & Bilpleie kan bruke vannet om igjen etter rensing.
– Da sparer vi vann, og vi belaster det kommunale avløpsnettet. Derfor er det gress på parkeringsplassene, hvor regnvannet renner ned i grunnen, sier Terje Olsen.
Sorry. No data so far.